The directional valve industry relies heavily on precise and reliable connections. Electromagnetic crimping machines have become vital in this field, providing high-precision solutions essential for the effective functioning of directional valves. This article explores the applications, working principles, advantages, and types of electromagnetic crimping machines, emphasizing their role in the directional valve industry.

Applications of Electromagnetic Crimping Machines in the Directional Valve Industry
Electromagnetic crimping machines are used extensively in the assembly of directional valves due to their ability to create robust and precise connections. The following applications highlight their significance:
Sealing process for moving cores

In the production process of solenoid-operated directional valves, one of its components, the end of the moving core, needs to be fixed in position with a crimping machine. Crimping machines squeeze the edges of the sleeve into the grooves of the plug and create a stable structure. At the same time, this process requires high precision of the crimping machine. Because if the precision is not enough, it may damage the processed parts after crimping.

Dot Crimp Moving Core Exterior
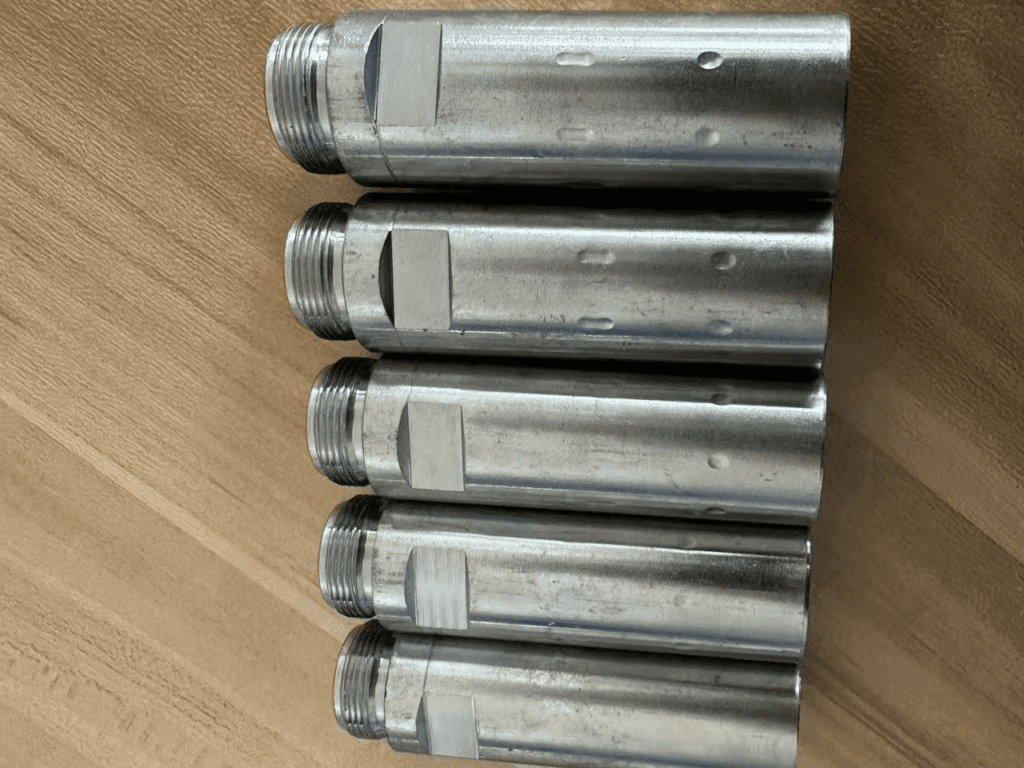
This process is in the form of crimping, which causes protrusions inside the pipe wall, thus effectively increasing the internal friction. It makes assembly work more efficient and easier than the old process.The old process was to install a friction plate between the slider and the pipe wall, and it was time-consuming and laborious to install.With the use of crimping machine processing, the friction plate installation work is eliminated, which can effectively improve the work efficiency by 120%.


Advantages of KANGMAI HYDRAULIC
Precision is paramount in the performance of crimping machines. Here’s why:
- Leak Prevention: In directional valves, even the smallest leak can cause significant issues. Precise crimps ensure a tight seal, preventing leaks and maintaining system integrity.
- Pressure Resistance: High-precision crimps can withstand the high pressures found in hydraulic and pneumatic systems, ensuring reliable performance under demanding conditions.
- Longevity: Precision in crimping extends the lifespan of directional valves by reducing wear and tear on the connections, leading to longer service intervals and lower maintenance costs.
- Safety: Accurate crimps are essential for the safe operation of directional valves, particularly in high-stakes applications such as aerospace and automotive industries.
Conclusion
Crimping machines are revolutionizing the directional valve industry by providing high precision, consistency, and durability in the crimping process. Their applications in hydraulic, pneumatic, and industrial machinery systems highlight their versatility and importance. Understanding the working principles, advantages, and types of these machines can help industry professionals make informed decisions to enhance their operations and improve the performance and reliability of their directional valves.